We work with strategic partners to deliver complete pyrolysis solutions, through feedstock preparation, drying, scrubbing, biochar management and energy production.
The equipment described here is manufactured by our partner, Woodtek Engineering.
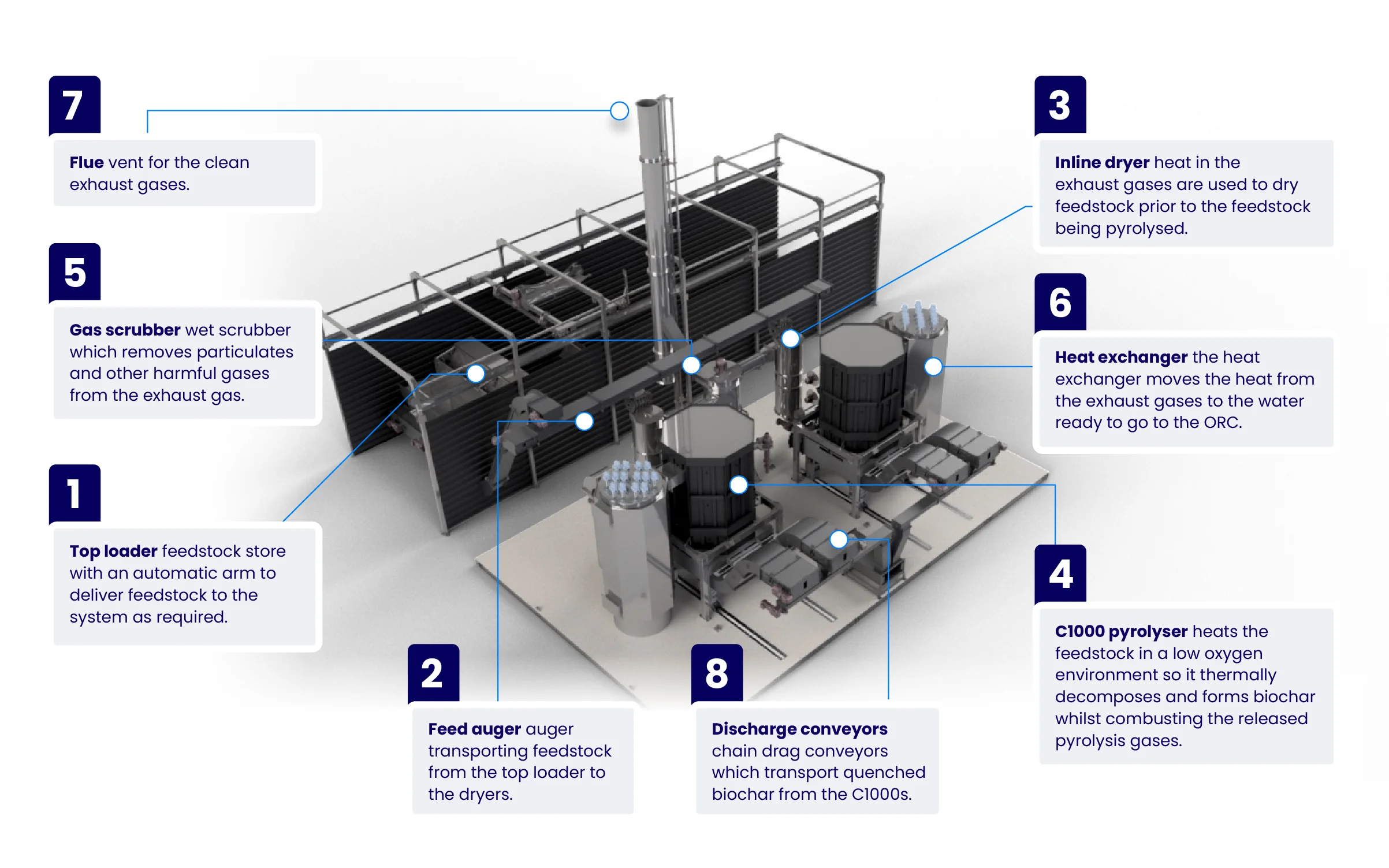
Key Features
Our pyrolysis plants transform waste biomass into valuable biochar which acts as a carbon sink - eliminating environmental harm and generating income.
Modular
Bespoke specification with proven cost-effective technology
Fully Automated
IoT for maximum performance with minimal supervision
High-tech emissions control
Scrubbers and emissions monitoring to ensure compliance
Multi-feedstock capability
Different biomasses can be handled
Control your output
Adjust parameters to control the carbon credits and energy you generate
Small footprint
Unique vertical design with a footprint of only
20 x 20 m
Why the C1000?
The C-1000 from Woodtek is the latest iteration of a design which has been successfully operating for over 5 years.
It has a unique vertical design, delivering many advantages over other approaches:
- Smaller footprint so it can can operate in more sites
- Easy maintenance reducing cost and interruption
- Tolerance of impurities such as stones or metal, meaning less downtime and repairs
- In-line dryer so high moisture feedstocks can be used with a minimum of energy
- Integrated scrubber resulting in minimal emissions
- High energy production due to minimal heat loss
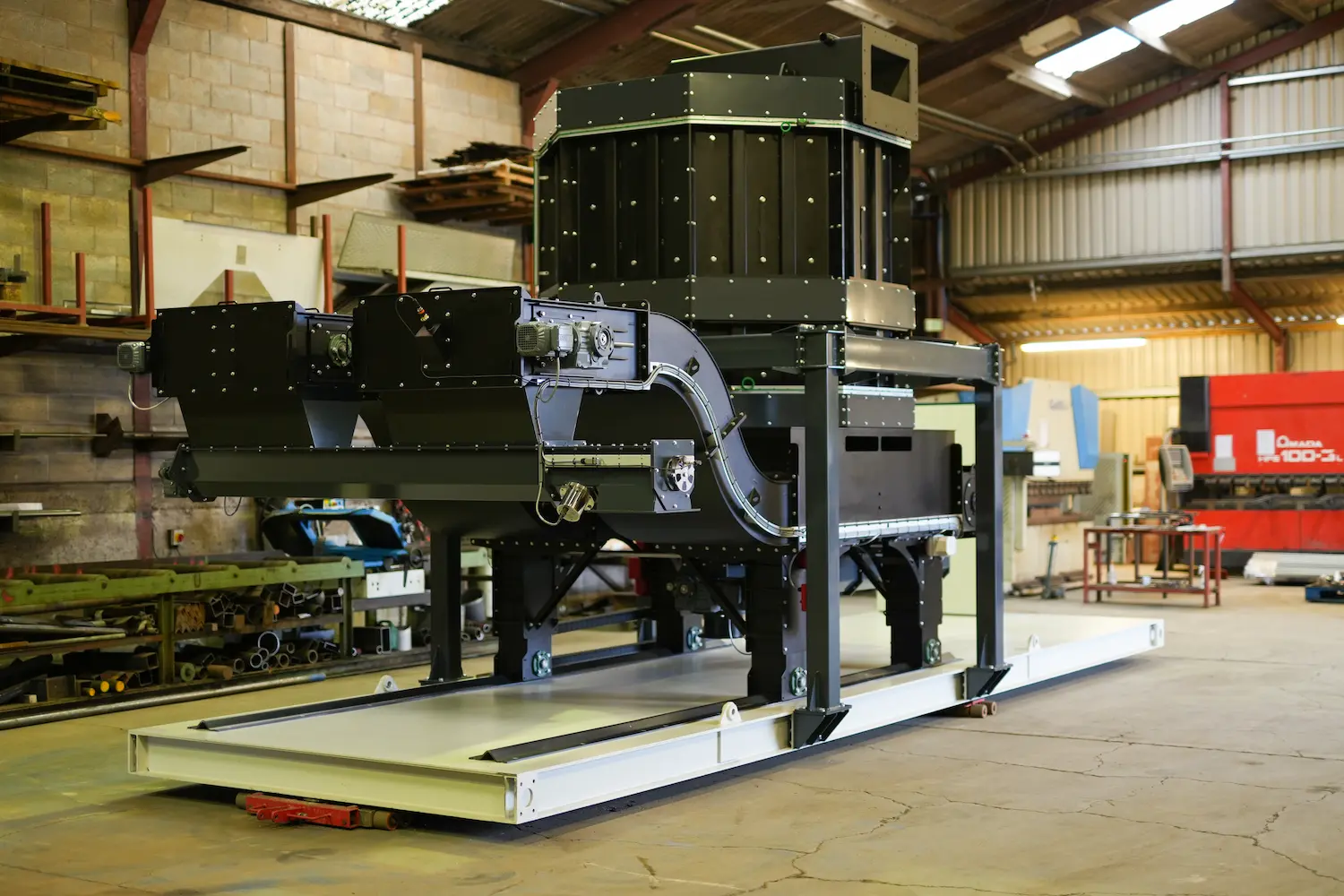
Add-ons we offer
These key modules are needed in most plants.
Add-ons we recommend
With the help of our strategic partners, we can guide you with the following add-ons to maximise the performance of your plant.
Design, installation and support
All our plants are installed and commissioned by qualified engineers, experienced with the equipment and the design of your site.
Commissioning ensures that the plant is working to all aspects of the pre-agreed specification and moves into production.
And once operational, our teams are available to support yours, conduct pre-planned maintenance and support you in every aspect of plant optimisation.
- Site design
- Installation
- Maintenance
- Remote and on site support
Sustainable development goals
Pyrolysis operations contribute to 8 of the 17 Sustainable Development Goals (SDGs).
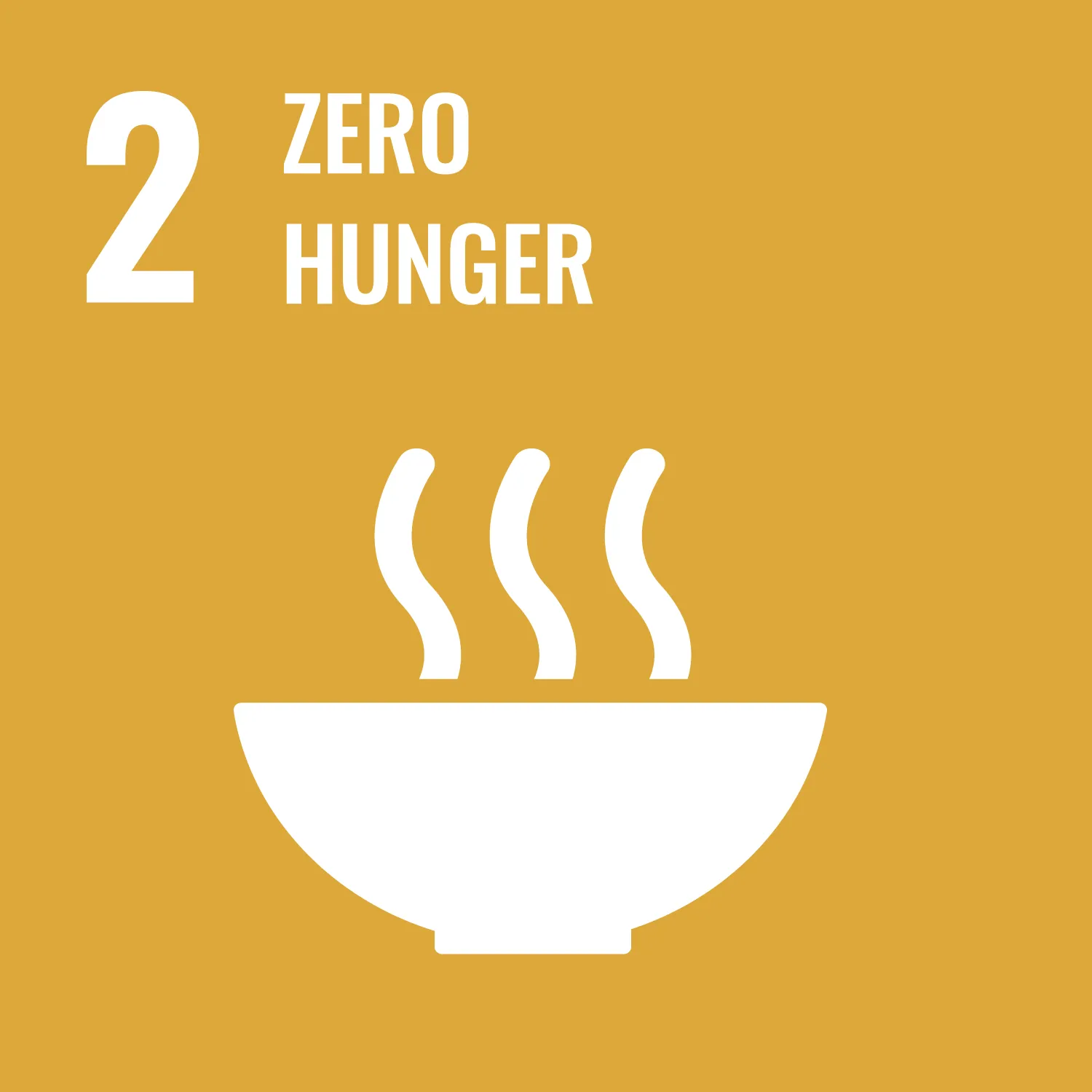
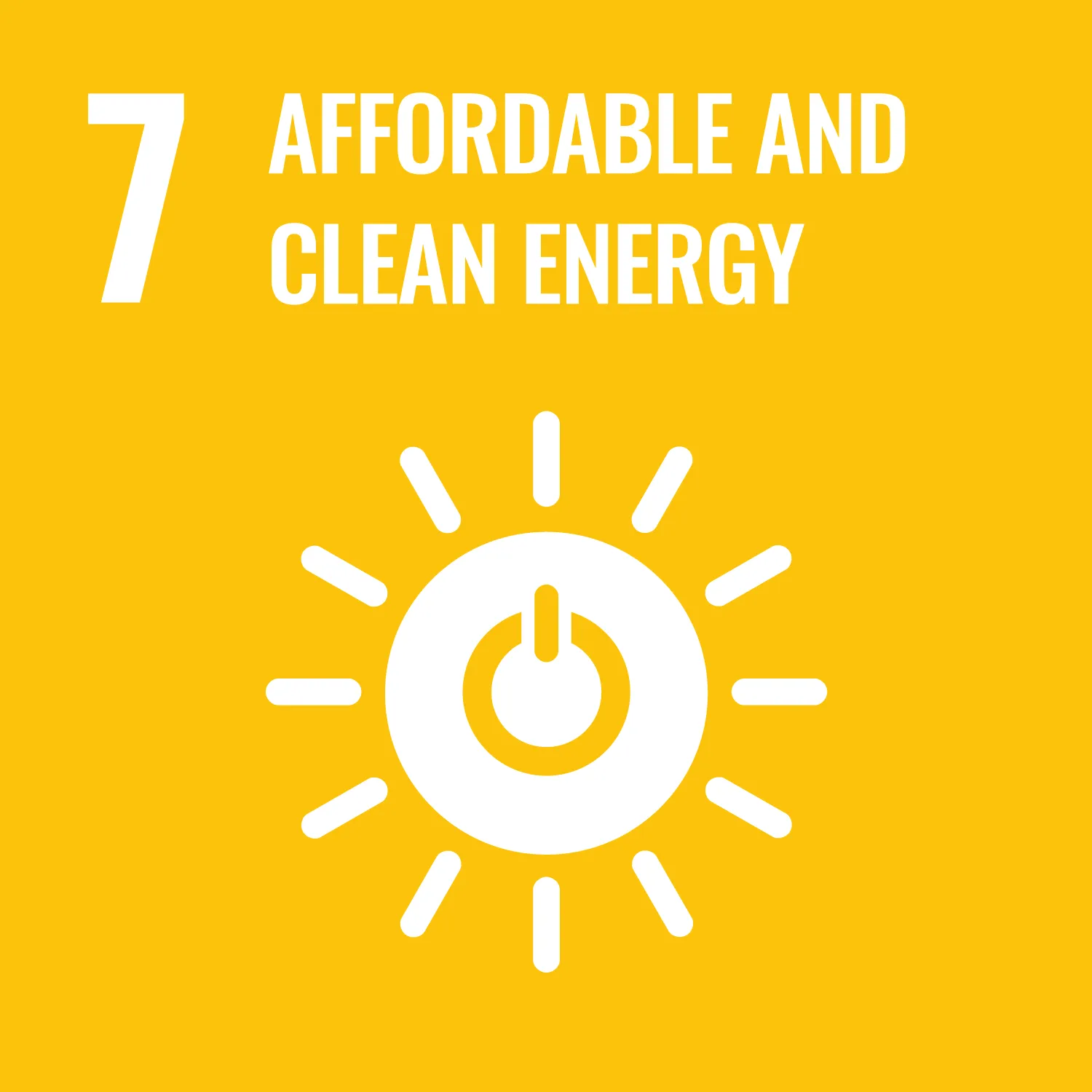
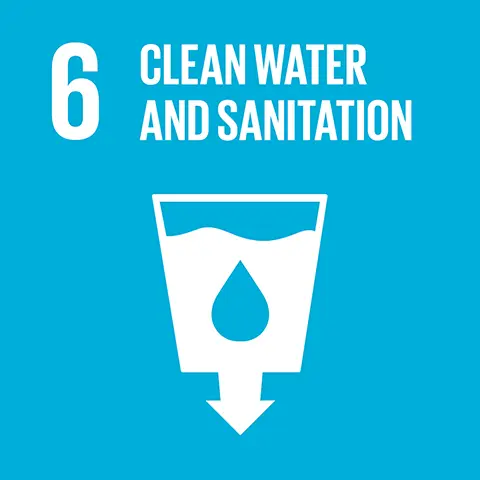
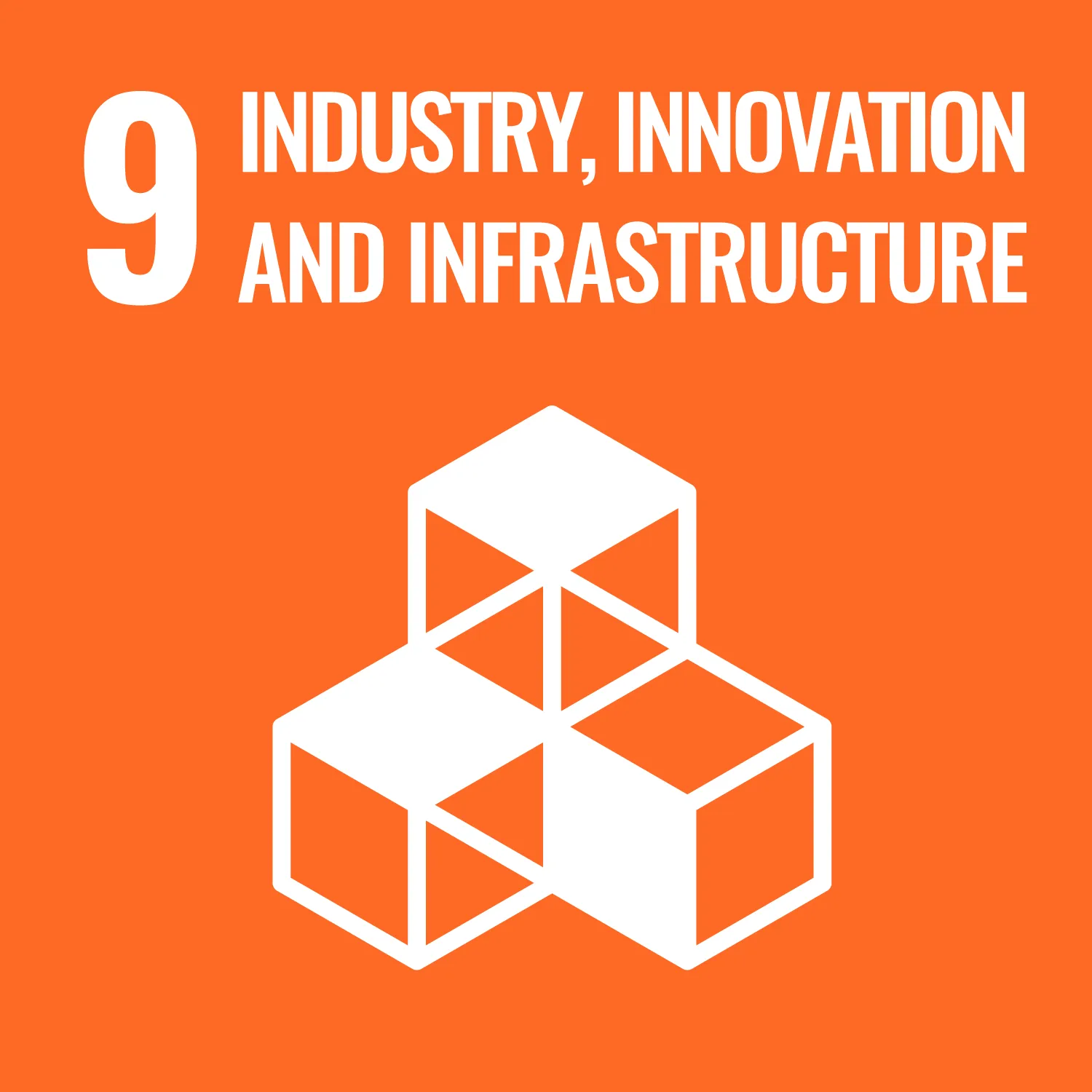
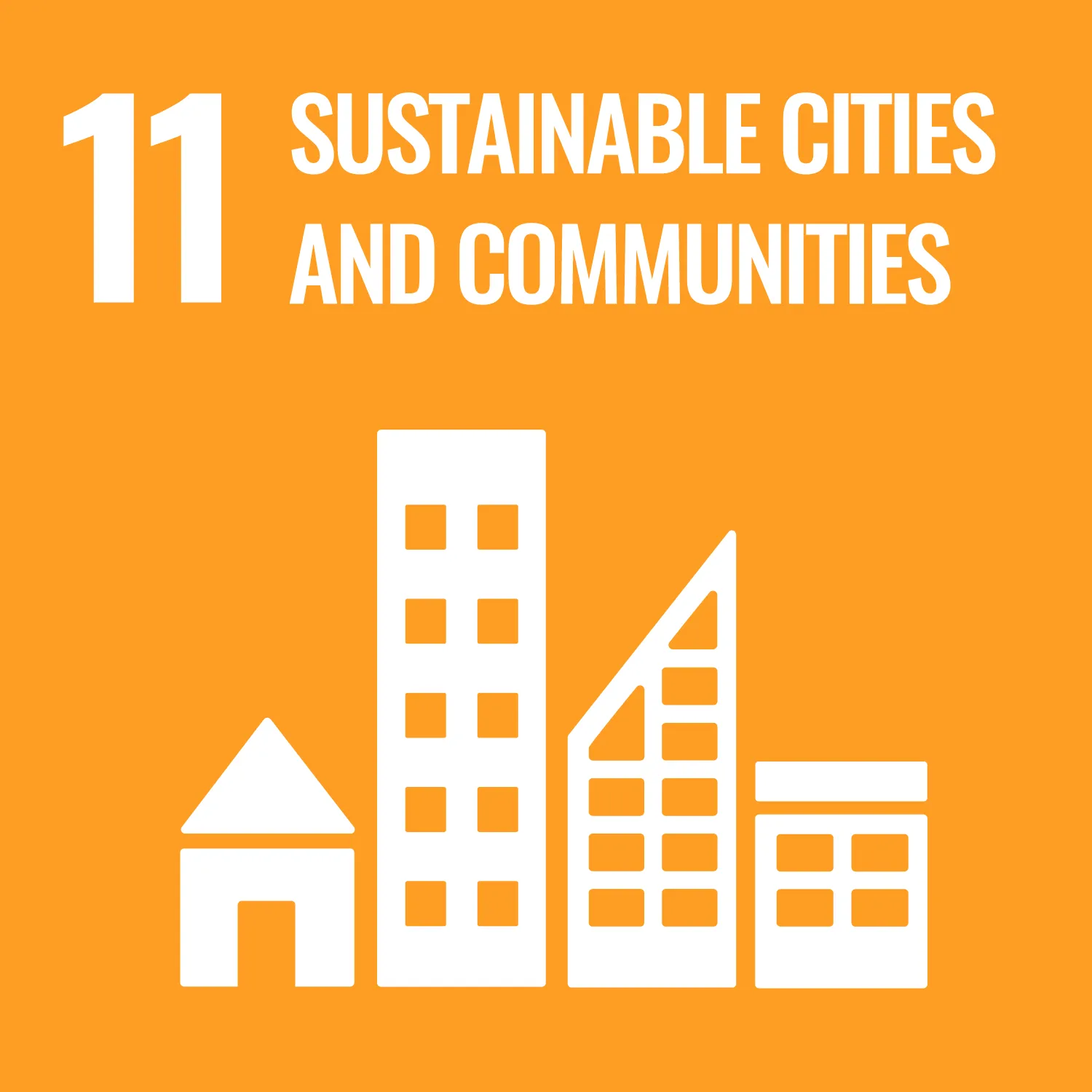
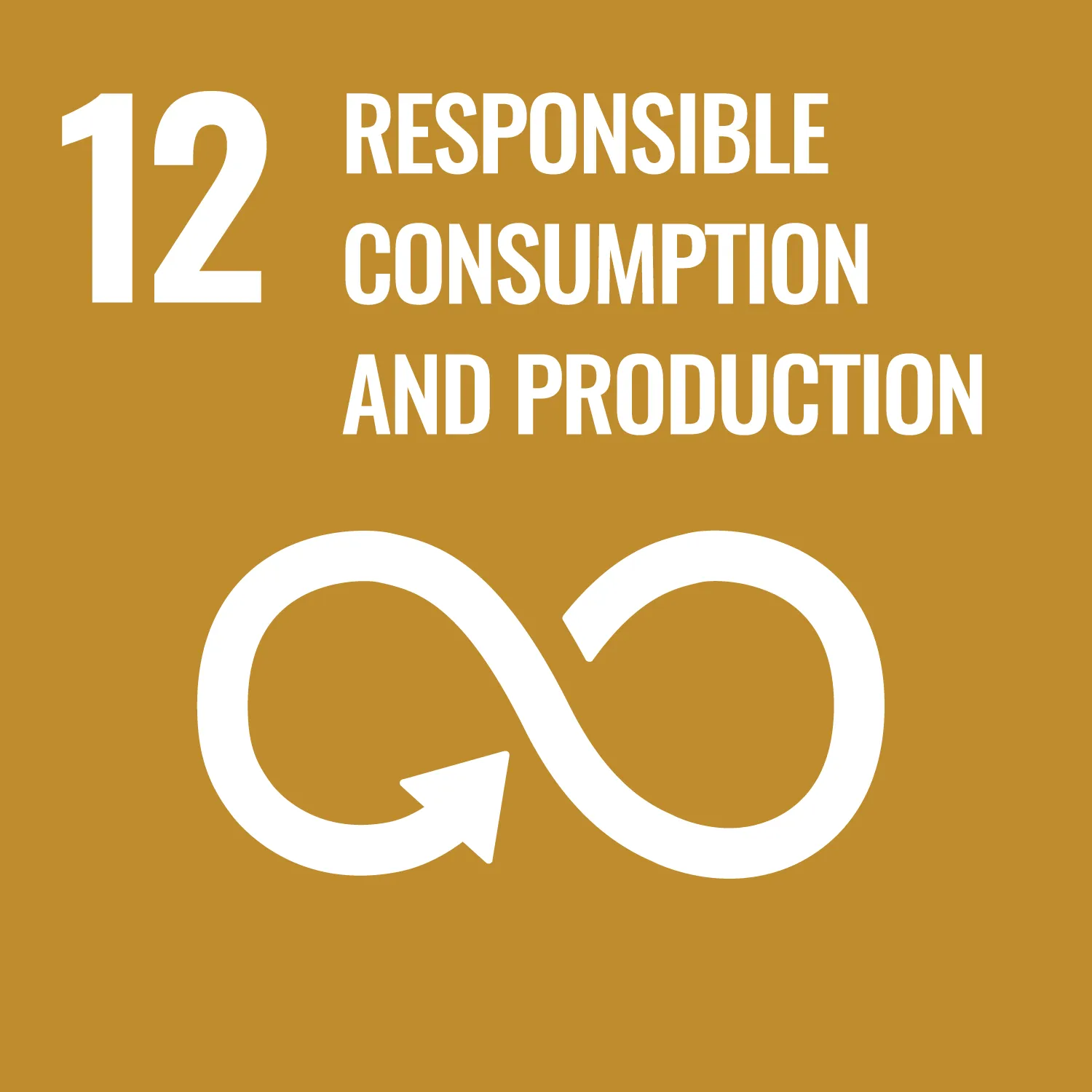
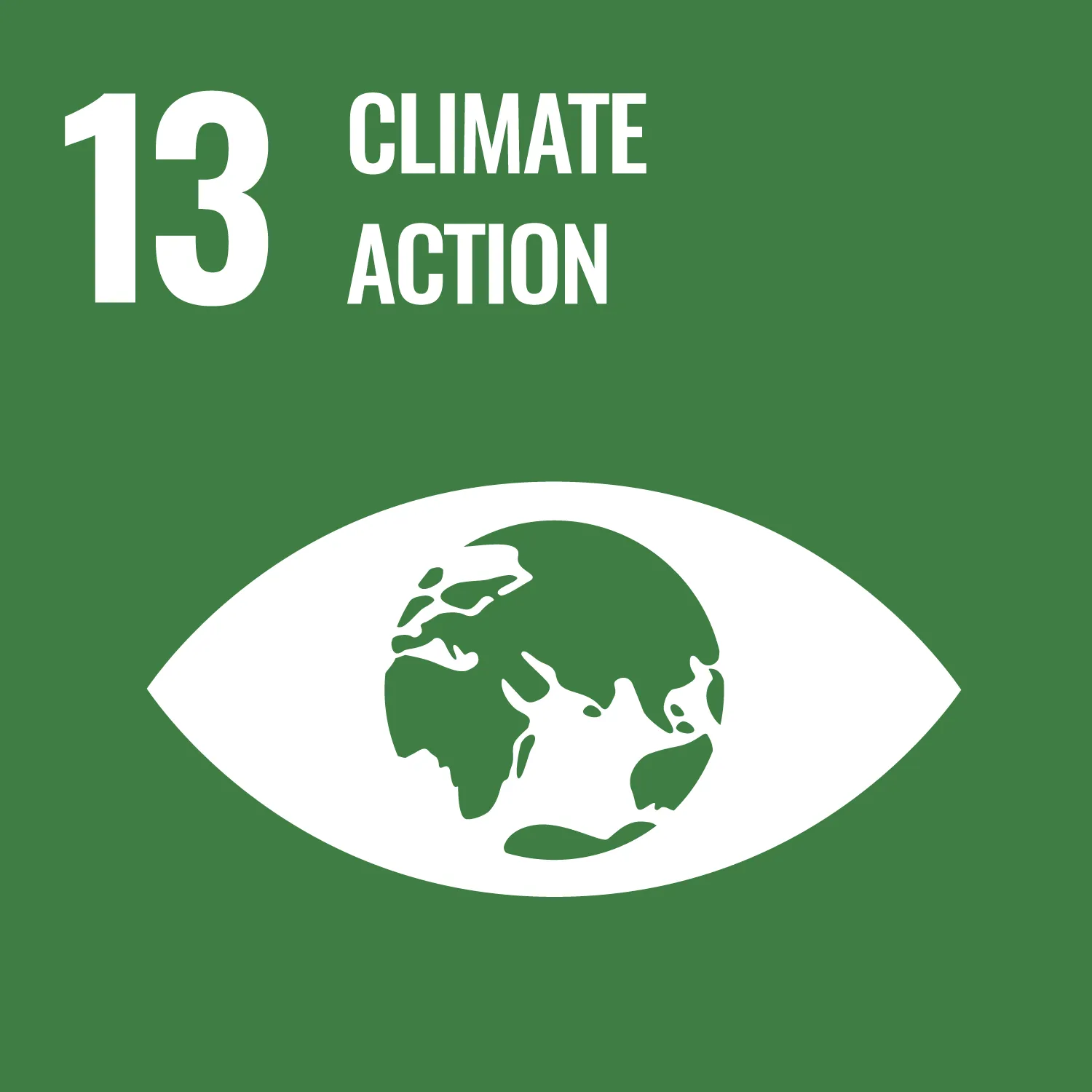
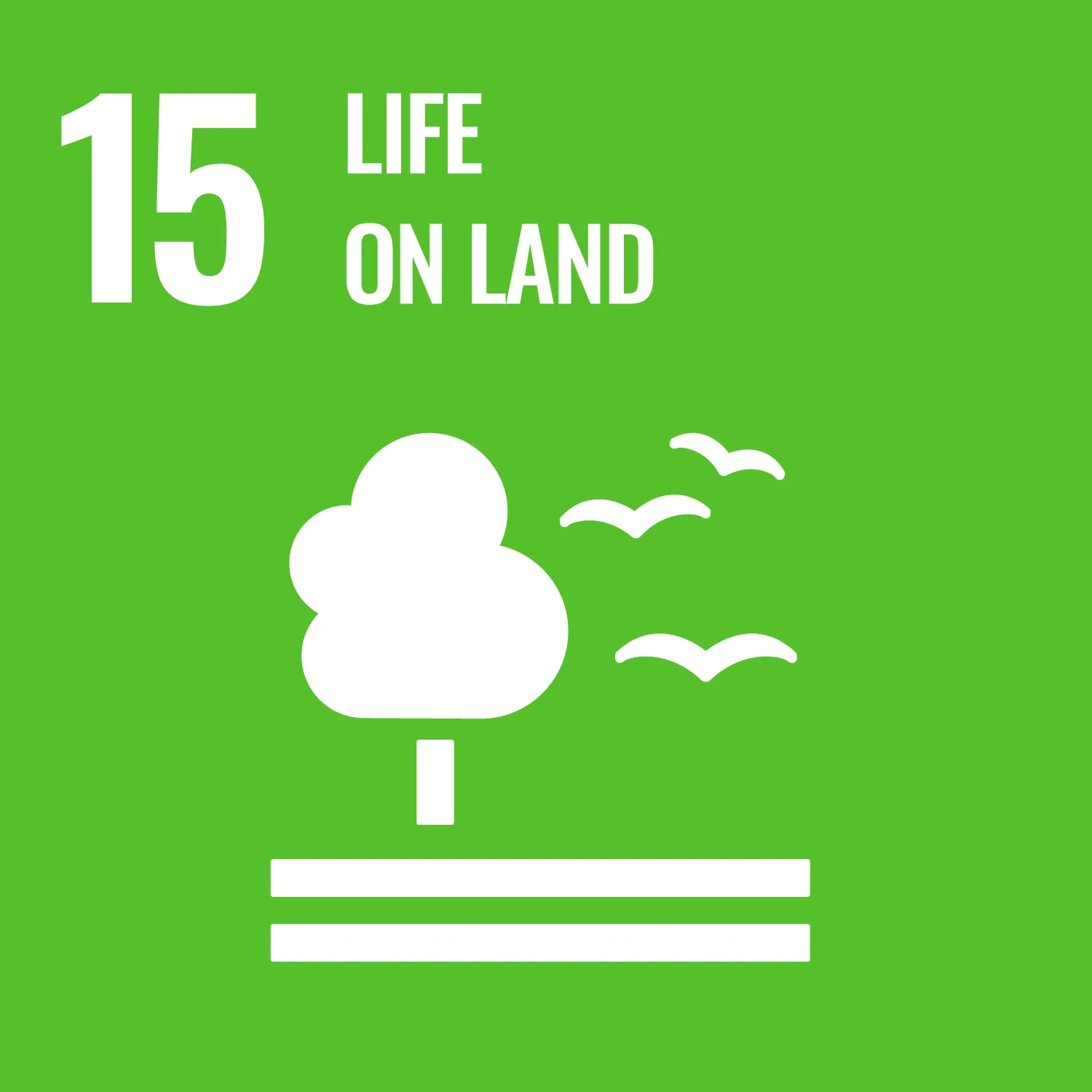
Want to know more about our technology?
Our experts can discuss how it works and how it may match your needs.